Introduction to 4 Core Cables with Vent Tubes
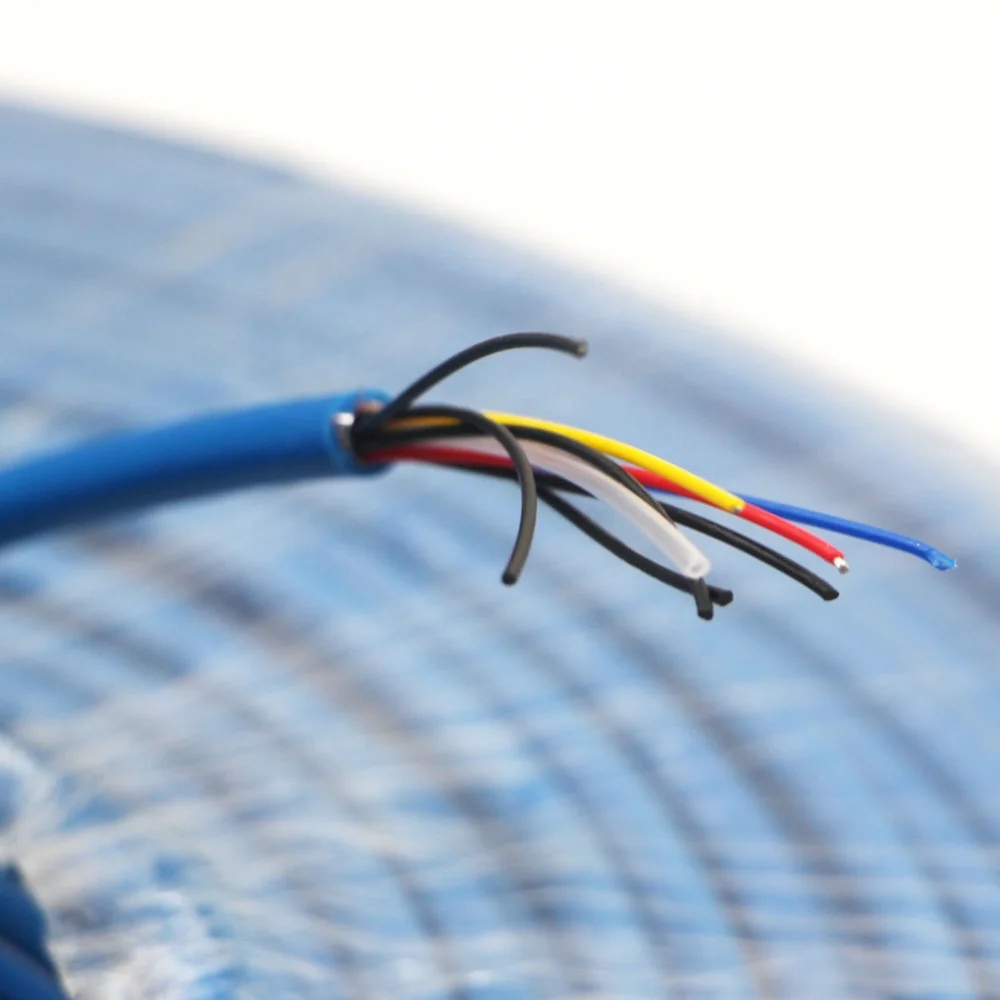
In recent years, 4 core cables with vent tubes have emerged as essential components in the field of engineering, particularly in applications related to water pressure measurement and fluid level detection. These specialized cables are designed to provide reliable and accurate measurement of various fluid parameters, which is crucial for numerous industries, including construction, environmental monitoring, and water resource management. The significance of these cables lies not only in their structural design but also in their functionality, which integrates advanced technology for enhanced performance.
The primary structure of a 4 core cable typically includes four conductors that enable the transmission of data related to electrical signals generated by pressure sensors. The inclusion of vent tubes facilitates the communication with pressure transducers in a manner that compensates for atmospheric pressure fluctuations. This design is particularly important in environments where water levels and pressures can change rapidly due to environmental conditions. As water instances are often subjected to atmospheric pressure variations, using cables with vent tubes ensures that measurements remain accurate and reliable, thus avoiding potential data inaccuracies.
These cables are extensively used in scenarios ranging from monitoring water levels in reservoirs, to managing pressure in industrial water systems. By maintaining a stable reference pressure through the vent tubes, engineers can obtain realistic measurements that inform decision-making processes. Furthermore, the versatility of 4 core cables allows them to be employed in a variety of installations, from surface-level applications to deep well systems, enhancing their utility across various engineering fields.
Ultimately, understanding the significance of 4 core cables with vent tubes is essential for professionals engaged in engineering and environmental sciences, as these cables not only improve measurement precision but also facilitate the effective management and oversight of water resources.
Understanding Water Pressure Measurement
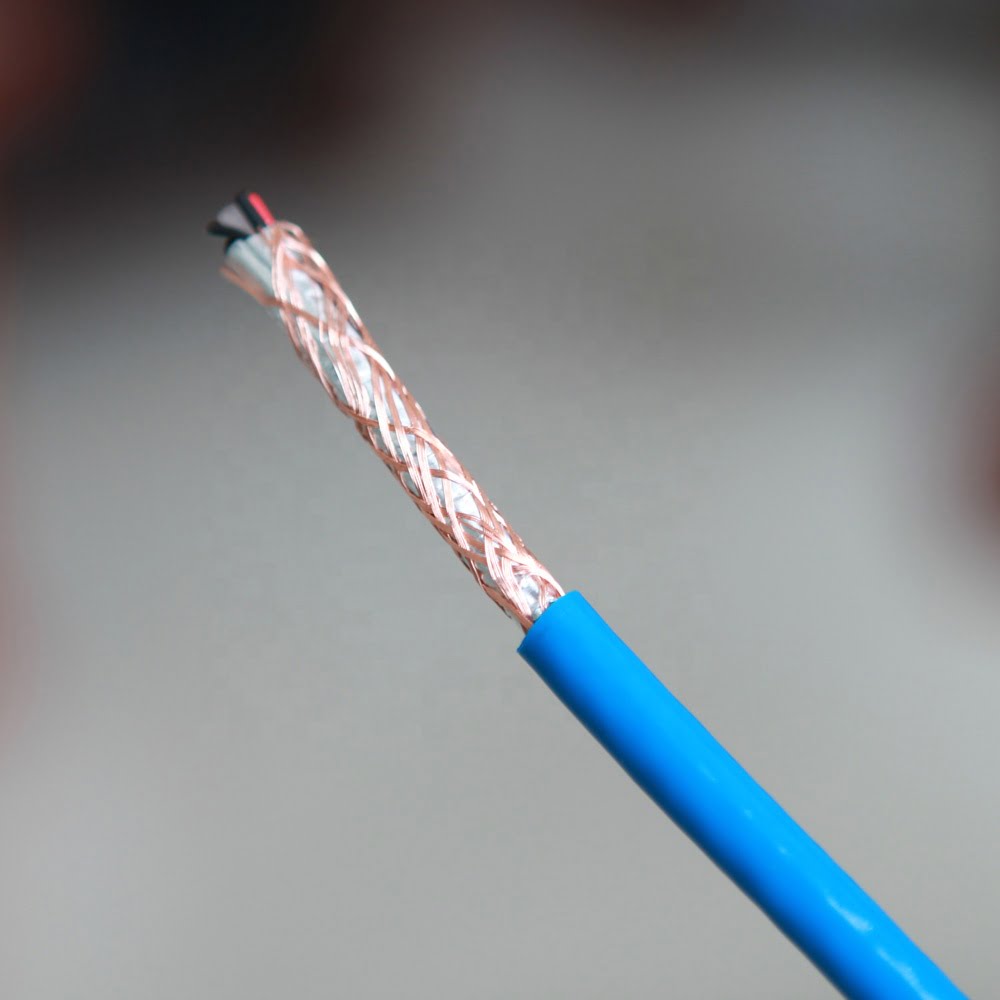
Water pressure measurement is a critical aspect in various industries such as hydrology, plumbing, and environmental monitoring. The concept revolves around understanding the force exerted by water, which can significantly influence system efficiency and safety. Pressure measurement is primarily concerned with quantifying the pressure in a water system, typically measured in pounds per square inch (PSI) or pascals (Pa). Əlavə olaraq, accurate readings are crucial for monitoring the integrity of water delivery systems and ensuring that pressure levels remain within safe operational tolerances.
Several types of sensors are utilized for measuring water pressure, with each possessing distinct advantages depending on the application. Common sensor types include piezoresistive, capacitive, and strain gauge sensors. Piezoresistive sensors are particularly valued for their accuracy and responsiveness, making them suitable for applications requiring precise pressure measurements. Capacitive sensors offer a different approach, as they measure pressure based on changes in capacitance, while strain gauge sensors function by measuring distortion in a material under pressure. Each sensor type provides unique benefits in terms of sensitivity and reliability, allowing for tailored solutions based on specific operational requirements.
To facilitate effective data transmission from these sensors to monitoring systems, 4 core cables are frequently employed. These specialized cables consist of four conductors, which enhance communication capabilities by allowing for simultaneous transmission of multiple signals. The design of 4 core cables, often incorporated with vent tubes, ensures that any pressure variations detected by the sensor are accurately and efficiently communicated to the monitoring systems. This seamless transfer of data is essential for establishing a comprehensive overview of water pressure conditions. Accurate water pressure readings play a vital role in preventing system failures, optimizing operations, and ensuring compliance with regulatory standards across various sectors.
Importance of Vent Tubes in Cable Design
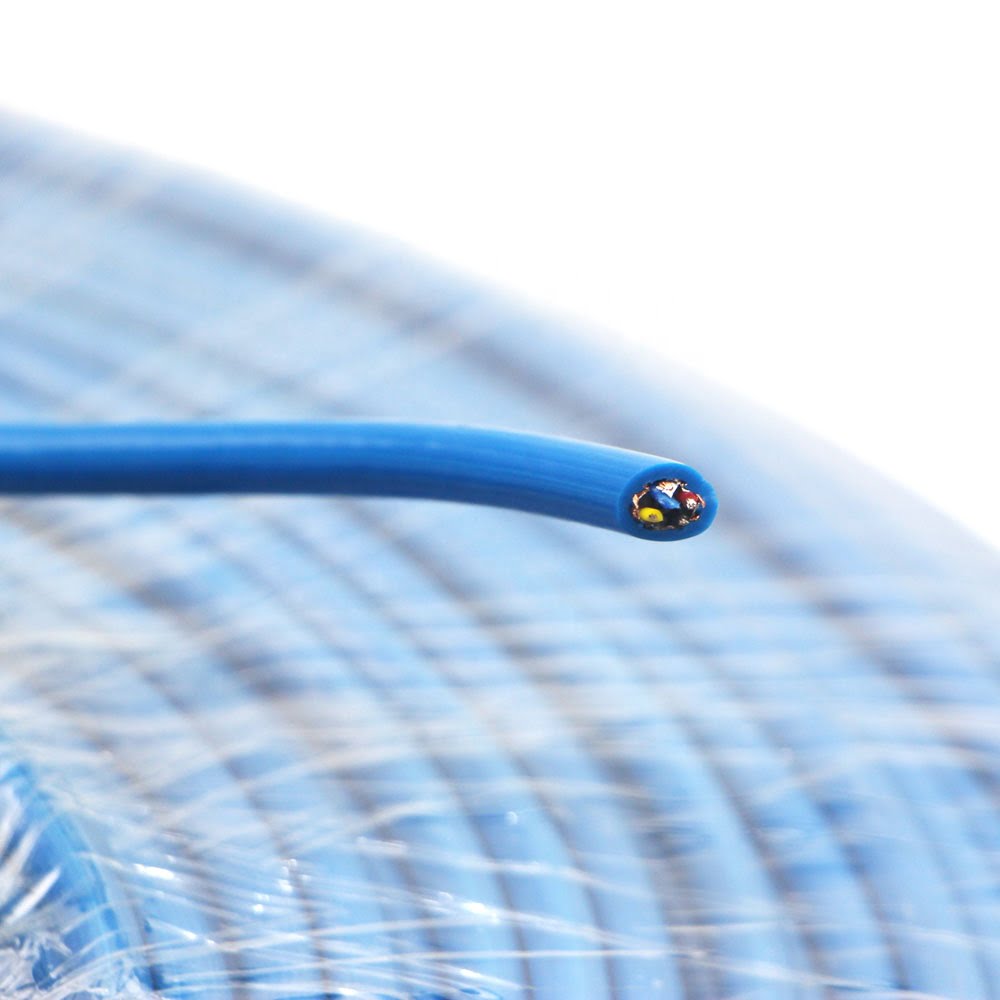
Vent tubes play a critical role in the overall functionality of 4 core cables, particularly those designed for water pressure measurement. These tubes serve as essential components that allow for accurate equalization of atmospheric pressure within the system. In setups where fluid level measurement is vital, such as in water management systems, the presence of vent tubes is crucial to ensuring that sensors and transducers can deliver precise readings.
The primary function of vent tubes is to allow air to enter the cable, which helps balance the internal and external pressures exerted on the sensing apparatus. When liquid rises or falls within the measuring device, variations in pressure occur. Without vent tubes, these changes can lead to erroneous readings, as the pressure differential may cause the sensors to respond inaccurately. By equalizing pressure, vent tubes help to mitigate these discrepancies, resulting in reliable and consistent fluid level measurements.
Furthermore, vent tubes are instrumental in preventing the build-up of negative pressure, which can adversely affect the performance of the pressure measurement system. In fluctuating environmental conditions, such as during heavy rainfall or rapid evaporation, ensuring that pressure levels remain stable is crucial. Vent tubes facilitate this stability by allowing for the escape of trapped air and moisture, thereby reducing the risk of pressure-related measurement errors that may otherwise compromise the data collected.
In summary, the incorporation of vent tubes in the design of 4 core cables enhances the accuracy and reliability of water pressure measurement systems. By effectively equalizing pressure and preventing atmospheric interference, these tubes ensure that measurement instruments operate efficiently, even in diverse and changing environmental conditions.
Mechanical Properties and Environmental Resistance
4 core cables with vent tubes are engineered to exhibit exceptional mechanical properties, making them ideal for various applications, particularly in challenging environments such as sewer and cleaning water systems. One of the standout features of these cables is their high mechanical resistance, which allows them to withstand significant physical stress without compromising their integrity. This durability is crucial in scenarios where cables may experience abrasions or impacts from external elements, ensuring consistent performance over time.
Another key attribute of 4 core cables is their flexibility. This characteristic facilitates easier installation and routing through tight spaces, which is often a requirement in sewer systems or cleaning infrastructure. The flexibility of these cables enables them to bend and contour around obstacles, ensuring that they can be deployed in a manner that minimizes stress points and potential failure points. This adaptability is beneficial in applications where traditional cabling might not be viable due to the non-linear layouts of sewage and water systems.
Üstəlik, 4 core cables display significant environmental resistance, which is fundamental in settings exposed to harsh chemicals and varying temperatures. The materials used in manufacturing these cables are designed to resist corrosion and degradation caused by exposure to toxic substances often found in wastewater or cleaning solutions. As a result, they maintain their functionality and longevity, providing reliable operation even in the most adverse conditions. The combination of mechanical strength and environmental resilience renders these cables an optimal choice for professionals focused on ensuring efficient water pressure measurement in challenging settings.
Electrical Specifications and Safety Standards
When discussing 4 core cables with vent tubes used for water pressure measurement, understanding their electrical specifications is paramount. These cables are designed to operate effectively under specific conditions, including an operating voltage typically ranging from 300V to 600V. This voltage rating ensures that the cables can handle the electrical demands common in water pressure measurement systems without compromising safety or functionality.
Another crucial specification is insulation resistance, which usually exceeds 1000 megohms at 500V DC. High insulation resistance plays a significant role in preventing electrical leakage, promoting overall system efficiency, and ensuring user safety. In addition to these core specifications, the cables often exhibit characteristics such as low capacitance, which further enhances signal integrity and reduces interference in measurement outputs.
Adhering to established safety standards is vital in the application of these cables. Cables designed for pressure measurement in water systems must comply with relevant national and international safety guidelines, such as IEC 60529, which addresses the degree of protection provided by enclosures (IP ratings). Ensuring proper insulation, moisture resistance, and cable integrity prevents potential hazards, including short circuits and electrical fires.
Üstəlik, these specifications contribute to the longevity and reliability of the cables in demanding environments. Məsələn, exposure to water and other harsh conditions can degrade inferior products quickly. Therefore, choosing cables with robust insulation and protective features is essential for maintaining operational effectiveness in water pressure measurement applications. Overall, a comprehensive understanding of the electrical specifications and adherence to safety standards guarantees the safe and efficient functioning of 4 core cables with vent tubes.
Core Configuration and Color Coding
The core configuration of 4 core cables with vent tubes used for water pressure measurement plays a critical role in ensuring accurate data transmission and efficient operation of the associated sensors. These cables typically feature conductors with a cross-section that is optimized for both flexibility and conductivity. The choice of the conductor’s size impacts the cable’s electrical resistance, allowing for minimal signal loss and increased responsiveness. For effective performance, the cross-sectional area must be sufficient to carry the expected load without overheating. Thus, manufacturers often recommend specific conductor sizes based on the anticipated range of water pressure measurements.
In addition to the conductor cross-section, the color coding of the cables significantly enhances the usability and safety of these components during installation and maintenance. The standard color scheme employs four distinct colors: qırmızı, yaşıl, ağ, and black. Each color is designated a specific function to streamline the identification process. Məsələn, the red conductor typically correlates with positive voltage supply, ensuring that users can easily connect the cable to the appropriate terminal without confusion. Green often represents the ground connection, which is crucial for safety and the prevention of electrical shocks.
Meanwhile, the white conductor is generally utilized for sensor signal transmission, facilitating data transfer to the monitoring system. The black conductor typically serves as the negative or return path for the circuit. This systematic color coding not only minimizes installation errors but also aids technicians during troubleshooting and maintenance activities. As a result, the clear identification of functions through color coding contributes to the reliability and efficiency of water pressure measurement systems. Overall, understanding both the core configuration and the associated color coding is essential for anyone involved in the installation or maintenance of these specialized cables.
Operating Conditions and Temperature Ranges
The operational effectiveness of 4 core cables with vent tubes largely hinges on the environmental conditions and temperature ranges within which they are deployed. These cables are engineered to withstand a diverse array of operating scenarios, making them suitable for various applications, particularly in water pressure measurement systems. Specifically, these cables exhibit remarkable durability under extreme temperatures that range from -30℃ to 75℃. This versatility ensures reliable performance in diverse environments, whether in frigid outdoor conditions or in relatively hot industrial settings.
Maintaining operational integrity under such temperature variations is vital for long-term applications, particularly in fields such as environmental monitoring, industrial settings, and civil engineering. At temperatures as low as -30℃, the physical and electrical properties of the cables remain intact, thereby preventing failures and ensuring consistent readings. Similarly, at elevated temperatures up to 75℃, the integrity of the 4 core cables is preserved, allowing them to function efficiently in high-stress environments aimed at precise water pressure measurements.
Üstəlik, these cables’ resistance to environmental factors such as humidity, abrasion, and chemical exposure contributes to their overall reliability and lifespan. The incorporation of vent tubes further enhances this design by preventing moisture ingress, which is crucial for maintaining the function of the underlying sensors. As a result, applications involving these cables can be deployed in varied locations, including underground installations and exposed outdoor environments, without compromising performance. Understanding these operating conditions and temperature ranges is essential for professionals tasked with selecting appropriate components for water pressure measurement systems, ensuring that the infrastructure remains robust over time.
Durability and Mechanical Performance Metrics
When evaluating the performance of 4 core cables with vent tubes, it’s essential to consider their durability and mechanical performance metrics. Two critical parameters to assess are the breaking load and the bending radius, both of which provide insights into the physical limits of these cables and their suitability for various applications.
The breaking load refers to the maximum load that a cable can withstand before experiencing failure or breakage. This metric is vital for understanding how much stress the cable can endure during its service life. For applications involving water pressure measurement, such as in deep-water installations, the breaking load becomes crucial in determining the cable’s ability to survive extreme conditions without compromising integrity. Depending on the application, engineers should select cables that not only meet the required breaking load specifications but also offer a safety margin, ensuring long-term reliability.
Another significant factor is the bending radius, which indicates the smallest radius that the cable can be bent without incurring damage. A small bending radius may lead to kinks or compromises in the cable’s functionality. It is particularly important when routing cables through tight spaces or around sharp corners. Understanding the minimum bending radius allows for better planning in cable installation, helping to avoid inadvertent damage that could lead to costly repairs or downtime.
In practical applications, both breaking load and bending radius should be taken into consideration together. Məsələn, when installing 4 core cables with vent tubes in environments where they may be subject to tension or physical constraints, both metrics will guide professionals to make informed decisions regarding cable selection and installation methods. Ensuring optimal performance under operational scenarios is foundational for effective water pressure measurements.
Conclusion and Future Perspectives
In summary, the exploration of 4 core cables with vent tubes for water pressure measurement has revealed their critical role in ensuring accuracy and reliability. These specialized cables are designed to withstand the harsh environments typically encountered in water pressure applications, significantly elevating performance standards. Throughout this discussion, we have highlighted how the unique design elements of these cables promote effective pressure transmission, while their durability ensures a long service life even under challenging conditions.
As industries increasingly rely on precise water pressure measurements for various applications, such as hydrostatic testing, aquaculture, and environmental monitoring, the importance of selecting the right cable cannot be understated. The integration of vent tubes into 4 core cables plays a pivotal role in alleviating internal pressures and minimizing the risk of measurement errors. This synergy between cable design and functionality is paramount for engineers and technicians involved in water management systems.
Looking towards the future, advancements in cable technology are expected to yield even more robust solutions. Innovations, such as improved materials that enhance the durability and flexibility of these cables, may significantly contribute to achieving heightened accuracy in pressure readings. Üstəlik, the potential for smart cable solutions, incorporating sensors and data transmission capabilities, could revolutionize the way water pressure is monitored and managed across various sectors.
Yekun olaraq, as we continue to advance in the field of cable technology, the prospects for new applications and improved reliability in water pressure measurement will expand. The emphasis on selecting quality 4 core cables with vent tubes will remain crucial to meet the demands of an evolving industry, ultimately leading to more efficient water resource management practices.